カーギル社の高い目標: 同社は人々に食料を供給するグローバルリーダになることを目指しています。世界70カ国に155,000名の従業員を擁し、農場から小売店およびレストランにいたるまでの完全に統合されたサプライチェーンを維持するこの農業複合企業は、その目標に向かって順調に前進を続けています。
同社の事業の主軸は、小規模な油糧種子圧搾工場やコーン油精製所、でんぷん精製所、製塩工場から、もっと複雑なエタノール蒸留やトウモロコシ発酵施設にいたるまでの食品加工分野になります。
工場全体のプロセス最適化を追求して、グローバルに構造化された継続的改善(CI)の取り組みがカーギル社で進行中です。
当然のことながら、プロセス制御の改善が高い優先順位を占めます。それは、プロセス制御がスループット、生産高、エネルギー消費、および生産品質に大きく影響するからです。「当社のCIプログラムの一環として、プロセス制御の調査が実施され、次に制御方法が標準化され、類似のプロセスを伴う多くのプラントに導入されて効率の改善に取り組んでいます」と、カーギル社の企業組織エンジニアリング&データ・サイエンス・チーム主任であるクリス・クリスティー氏は述べています。
ある程度までの成果はありました。クリスティー氏はさらに次のように説明します。「私たちはこの調査を続けてきて、制御ループを実装し、そこから得られる値を観察してきました。しかしながら、さまざまな構造的およびスキルセット上の理由からその結果がサステナブル(持続可能)ではないことにすぐに気がつきました。」
カーギル社のプロセス最適化の取り組みから得られた結果を良い状態で維持するには、制御ループのパフォーマンスモニタと高度な診断ソリューションが必要でした。クリスティー氏と彼のチームは、オプションの概念の評価と選択、および試験的な概念実証を実施し、現在、ロックウェル・オートメーションのEncompass™製品パートナであるControl Station社のPlantESPをカーギル社の世界中の70以上の製造施設に導入しています。
進歩の限界
カーギル社の標準的な製造工場では、規模に応じて何十、何百もの(何千単位ではないにしても) PIDコントローラを使用して生産を調整しています。すべてのコントローラが自動モードで動作するように方針は確立されていましたが、プロセス制御エンジニアがプラントを自動モードで運転してみると、一部のコントローラはマニュアルモードに戻っていたことが後になって判明しました。その結果、最適化の取り組みから得られた成果は失われました。
その当時はモードのステータスを追跡する方法は存在せず、またプラントレベルでのアカウンタビリティも欠如していたため、パフォーマンス分析やPIDチューニングなどの処置は、問題が発見された後にならないと実施されませんでした。「油糧種子圧搾および精製などの当社の比較的単純なプロセスの場合は、プロセス制御の担当者がいなかったため、私たちはそれらの事が協調して行なわれているかどうかを観察することはありませんでした」と、クリスティー氏は説明します。
調査は複雑で時間がかかる作業で、一般的にトレンドデータのパターンを観察し、手作業で複数のトレンドを比較対照し、どのコントローラが問題を引き起こしているかを特定する作業が含まれます。「このような手作業での分析アプローチでは信号ノイズも考慮にいれる必要があり、そのことが一層パターンの特定を困難にします」と、Control Station社の技術担当副社長であるボブ・ライス氏は述べています。
複数の生産施設にわたってパフォーマンスの一貫性をできる限り維持するために、カーギル社ではループパフォーマンスの可視性を向上させ、切迫した問題を検出し、トラブルシューティングに必要な診断を提供し、是正処置を推奨する制御ループ・モニタ・ツールが必要でした。
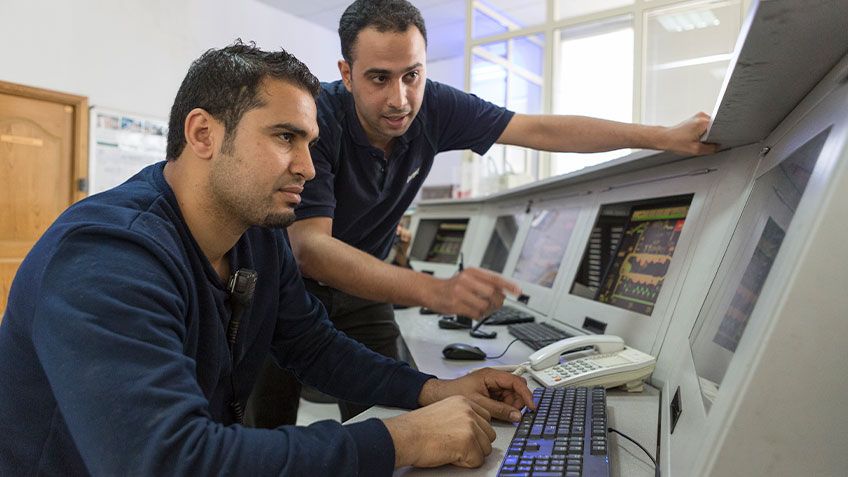
ソリューションの探求を開始
2015年半ばに、クリスティー氏は9つの異なるソリューションを比較する実現可能性調査を開始しました。それらのソリューションの2つが、カーギル社の機能的要件とユーザインターフェイス要件に一致し、望ましい技術的評価基準を備えていたため、この2つがカーギル社の既存のOSIsoft PIデータ履歴管理(ロックウェル・オートメーションのEncompass™製品パートナであるOSIsoft社が提供)との互換性を評価されました。
最終的に、カーギル社はControl Station社のPlantESPを選択しました。選択理由は、導入、構成および使用の容易さとOSIsoft PI-SDKを介してカーギル社のデータ履歴管理に直接接続できること、および、複数のプラントの接続をサポートする一元管理されたサーバが利用できることでした。
さらに、PlantESPの機能はロックウェル・オートメーションのソリューションを補完しています。カーギル社は、主としてAllen‑BradleyのControlLogix制御システムを使用して油糧種子プラントを運用しており、一部のPLCはPLC-5まで遡ります。また、カーギル社はロックウェル・オートメーションのプロセッサ、ドライブ、およびヒューマン・マシン・インターフェイス(HMI)ソフトウェアも使用しています。
このソフトウェアは、制御ループのパフォーマンスの問題を特定、分離、および特長づけるために主要業績評価指標(KPI)を使用し、高度な診断および工場全体のプロセス最適化を提供します。このソフトウェアは、カーギル社が数多くのローカルプラントの履歴管理から得られた生のプロセスデータを一元管理し、ダッシュボードからアクセス可能なすぐに使用できる情報に変換するために役立ちました。
このソフトウェアは、PIDコントローラのパフォーマンスを解析し、機械的、PIDチューニング、またはプロセスの相互作用の問題によって引き起こされる変化を識別します。このソフトウェアは高度なフォレンジックユーティリティを使用して根本原因の解析を簡略化し、プラントをその他のプラントと比較した相対的なパフォーマンスを査定するツールをカーギル社の経営陣に提供します。
「使いやすさは技術の重要な側面の1つです。それは、高度な解析ツールの導入時にしばしば連想される「懸念要素」を本質的になくすからです」と、Control Station社の社長兼CEOであるデニス・ナッシュ氏は述べています。
実証のための予備試験
予備試験は2015年末にカーギル社の以下の3つのプラントで、重要度の高いループを使用して開始されました。
- ミズーリ州カンザスシティでの油糧種子圧搾プラントでは104のループ
- ネブラスカ州ブレアのコーン油精製プラントでは250のループ
- オランダのでんぷん精製所でのユニットオペレーションでは23のループ
また、以下のような2つの作業が同時に発生します。
- 世界中の70以上のプラントに対応する青写真の役割を果たす中心的なアーキテクチャの開発
- 各現場のローカルデータ履歴管理から中央サーバにデータを抽出し、中央サーバ内から分析のためにプラントを構成
2016年初めまでに、3つの施設のすべてで一元管理されたサーバ上の単一のインスタンスで正常に動作を開始しました。
その結果、カーギル社は2020年に完了が予定される全面展開に向けてPlantESPの導入を開始しました。これまでのところ、PlantESPは油糧種子圧搾、精製および製塩などの製造工場を含む60以上のプラントに導入されています。各現場では、データがどこから来て、その結果何をすべきかについてプラントチーム全員がトレーニングを受けています。
一貫性のあるプロセス最適化の実現
カーギル社は現在、PlantESPを使用している施設ではPIDコントローラのパフォーマンスを基準通りに維持することができます。継続的なループ終了の基準が維持できない場合は、自動的にレポートが生成され、現地スタッフはコントローラが手動モードに入る前に適切な対策を講じることができます。
ライス氏は次のように述べています。「これによって、カーギル社は95%以上の時間でコントローラを「通常」モードに維持することができ、そのことがオートメーションへの同社の投資価値を高めています。
また、クリスティー氏は次のように述べています。「当社の制御ループのパフォーマンスの可視性が向上したためプロセスの可視性も高まり、こうした制御方法から投資価値を以前より高く維持できるようになりました。このことから、生産高と効率もプロセススループットの増加とともに向上しています。」
ノーマル時間割合(Percent Time in Normal)や全体的なループ健全性(Overall Loop Health)などの単純な評価基準がローカルプラントの運用チームのさまざまなメンバーからも使用可能になり、指揮系統の上層部へと報告されます。振動尤度(Oscillation Likelihood)や静止摩擦尤度(Stiction Likelihood)などの高度な評価基準も、高度なトラブルシューティングに使用可能です。
毎日および毎週のプラント生産ミーティングでは、問題発見時に何をすべきかに関するカーギル社のガイドラインが議題に組込まれました。
ローカルおよび中央での制御リソースの使用率が向上しました。不一致が特定された場合はソフトウェアが予防的に警告を発し、新しいパラメータの推奨を含むチューニング評価を提供するため、特定のループのチューニングの必要性は減少しました。
ソフトウェアが毎日の出力変化を自動的に取得しモデル化を行なうため、エンジニアリングチームが衝撃試験を実施する必要はなくなりました。3~4カ月かかる手作業での分析のかわりに、ツールのフォレンジック機能が同社の工場全体の最適化の取り組みを支援します。
さらに、プログラミングエラーも検出可能になりました。非常によく似たコントローラと制御ループが搭載された型抜きデッキのレベルバルブでは、フラグを立てて、PlantESPがプラントオペレータに1つのデッキのレベルが他のデッキより頻繁に変化していることを知らせます。1つのプログラミングが他と異なっていることが判定され、プログラムを修正することによって問題が解決されます。
また、これまで発見されずに見過ごされていた問題も検出されるようになりました。プラントオペレータが大規模なプロセス障害を徹夜で解決したような場合には、次の日の評価基準にエラーが表示されます。調査によってヒューマンエラーとトレーニング不足が根本原因であることが明らかになると、これらの要因に対して速やかに対策が講じられます。
クリスティー氏は同様の成果を求める製造メーカに対して、関係者にプロセス制御の価値を理解させること、現場チームが評価基準に対して説明責任を持つこと、他の制御ループを追加する前に重要度の高い制御ループから開始することなどを奨めています。