Tracking key metrics like OEE, cycle time, lead time to produce, downtime, first pass yield, throughput, yield rate, inventory turnovers and energy efficiency are some crucial performance indicators enabling manufacturing companies to measure the effectiveness of these manufacturing technologies to drive continuous improvement.
1. With rising customer expectations and regulatory requirements, what are the challenges facing Asia Pacific manufacturers?
Manufacturing companies in Asia Pacific are struggling with significant challenges on multiple fronts, driven by rising customer expectations and stringent regulatory requirements.
Inflexibility
The agility and flexibility to sense and respond to market fluctuations and changing customer demands. Companies need responsive supply chains and integrated planning systems.
Downtime
Manufacturing being the ‘heart’ of the supply chain, any unplanned downtime severely disrupts production schedules and increases costs. This adversely impacts the entire supply chain. Companies are compelled to implement predictive maintenance strategies using IIoT and real-time analytics to foresee and prevent equipment failures.
Sustainability & Regulatory Compliance
Adhering to stringent quality standards and adopting sustainable manufacturing practices is another critical challenge. They are driven by both local and international regulations and customer preferences for environmentally friendly products. Manufacturers must implement sustainable processes, reduce waste, and improve energy efficiency, which can involve significant upfront investments but are crucial for long-term viability.
Mass Customization
The demand for lot/batch size one, or mass customization, will grow exponentially in the B2C manufacturing industry segment. This necessitates investments in advanced manufacturing technologies and modular production lines, allowing for the efficient production of customized products without sacrificing economies of scale.
Technology Investments
Balancing these demands with cost sensitivity in a labor-intensive market such as Asia Pacific, while aiming for a high return on investment, adds another layer of complexity and manufacturers end up in a state of technology paralysis. Strategic investments in technology and continuous workforce awareness are necessary to meet these challenges while maintaining profitability and competitive advantage.
2. What role does technology play in optimizing production operations?
Manufacturing technologies undoubtedly play a pivotal role in optimizing production operations by enhancing efficiency, productivity, and flexibility. By leveraging technologies – including production automation, robotics, autonomous guided vehicles, manufacturing execution systems (MES), supply chain planning and real-time monitoring with AI-enabled data analytics – they can help to streamline processes and improve overall performance for manufacturing companies across industry verticals. Manufacturing companies have seen significant improvements in both revenue and profit performance index following these adoptions.
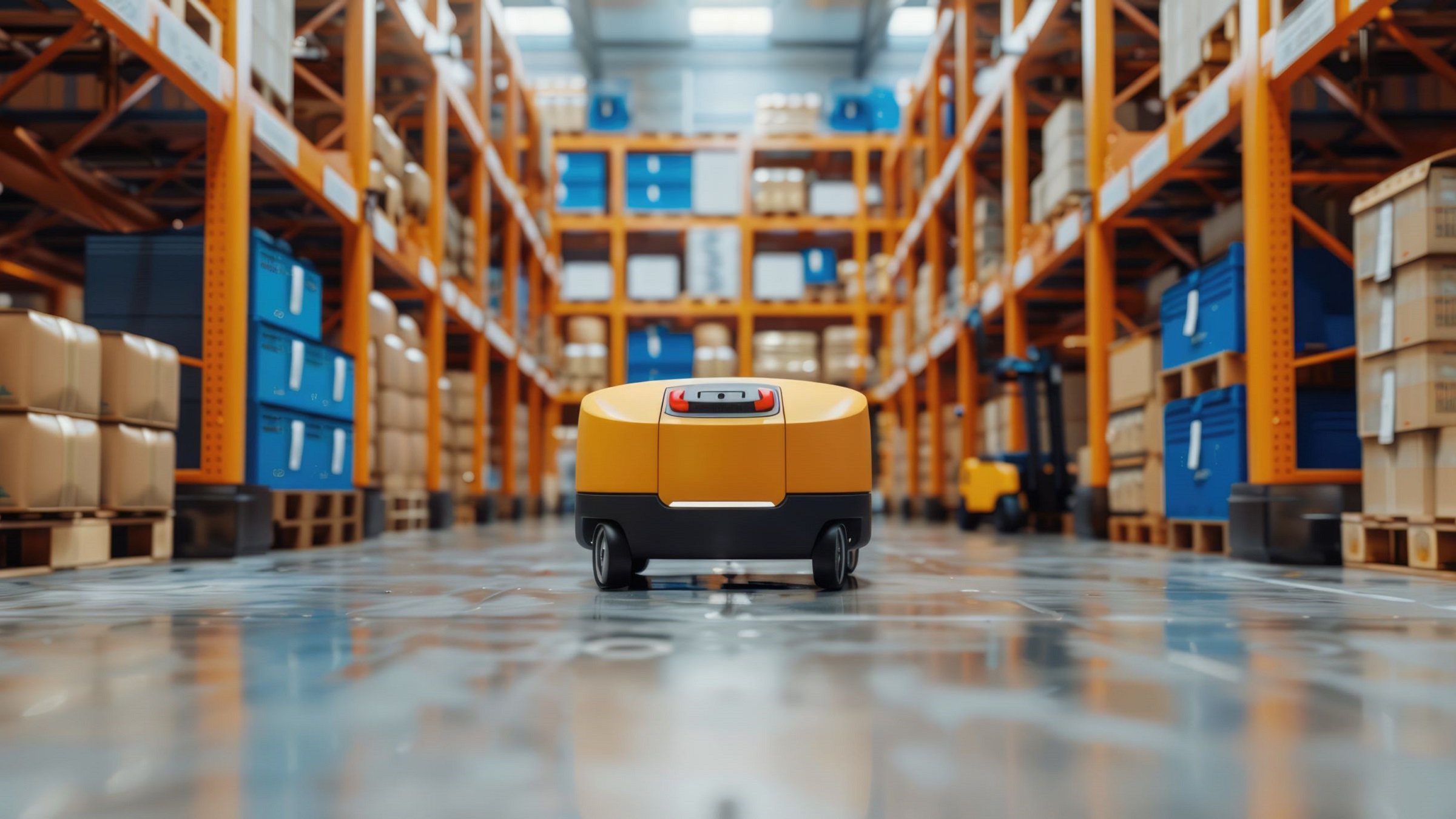
3. How should manufacturers balance cost reduction while maintaining product quality and customer satisfaction?
Quality undoubtedly comes at a cost. The cost of prevention, that is ensuring good quality from the start, is always less than the cost of correcting defects later.
During my engineering days, I was deeply influenced by Dr Genichi Taguchi’s concept of ‘quality by design.’ This principle emphasizes embedding quality control in R&D and product design (APQP, PPAP, FMEA, HACCP etc.), aiming to create products that achieve zero defects once they hit the shop floor.
With today’s technological advancements, this ideal can become a reality. Investing in digital engineering, digital production automation, and digital production operations (MES, QMS, data analytics etc.) technologies bring Dr Taguchi’s vision to life with cost-effectiveness and scalability.
These investments enable precise, consistent production processes, reducing human error and enhancing efficiency. They help to ensure that quality is built into the product from the start, reducing the need for costly corrections, and ultimately satisfying customers. By adopting this approach through prevention and appraisal, manufacturers can achieve greater economies of scale and stay competitive while delivering top-notch products efficiently.
4. You mentioned that manufacturing plants need agility and flexibility to stay competitive. How does MES combined with powerful analytics help?
The MES serves as the manufacturing operating system for any plant floor. It holds the data to help organizations make key tactical decisions impacting their top and bottom line.
- Improved Agility and Flexibility: Immediate visibility into production processes for quick adjustments
- Dynamic Scheduling: Flexible production scheduling to adapt to market demands
- Predictive Maintenance: Forecasting equipment failures to reduce unplanned downtime
- Predictive Quality Control: Early detection and correction of quality issues
- Debottlenecking: Identifying and addressing inefficiencies to improve operations
- Optimizing Cost Variance: Analyzing cost of conversion to reduce waste and operational costs
One example is contextualizing energy intensity (WAGES usage data) sourced from an energy management system against MES production data. The analysis can produce amazing insights into the impact of energy usage on cost of conversion, defects analysis and profitability of a particular SKU.
By integrating MES with analytics, manufacturing plants can enhance operational efficiency, maintain high quality, and remain responsive to market changes, ensuring competitive advantage and customer satisfaction.
5. How is Rockwell Automation helping manufacturers to drive operation excellence and generate business value?
Rockwell Automation is strongly positioned to drive operation excellence and generate business value for manufacturing companies through its comprehensive spectrum of technology solutions, from sensors and controllers to SCADA, MES, ERP, SCM, Industrial Data Ops, and cybersecurity. As a provider in each of these segments, Rockwell Automation serves as a one-stop business transformation partner for manufacturers' technology needs, both now and into the future.
Let me give you two customer case studies to illustrate:
One notable customer, a leading automotive component manufacturer in India, faced significant challenges with efficiency and productivity due to their 100% paper-based plant operations. Traceability was crucial for compliance and winning new business. Rockwell Automation's cloud-based MES, the Plex Smart Manufacturing Platform™, was selected to address these challenges. Enabling enhanced efficiency and boosted productivity by automating processes and providing real-time data insights for their plant operations across four geographically spread across India. It will also ensure comprehensive traceability, enabling the manufacturer to meet regulatory compliance requirements and secure new business opportunities.
Another customer, a leading electric vehicle (EV) battery manufacturer in Southeast Asia, struggled with a monolithic legacy MES that could not adapt to their rapidly scaling business. They needed a more scalable, secured, and commercial off-the-shelf MES platform. Rockwell's MES platform was the ideal solution to meet their needs. It provided the scalability needed to support their growth and the agility to adjust to changing business needs. The MES platform is enabling them to drive smoother operations, reduced downtime, and increased overall efficiency, directly contributing to the company’s growth trajectory.
In both cases, we helped manufacturers overcome specific challenges and future-proof their operations, by addressing specific challenges such as outdated manual processes and inflexible legacy systems.