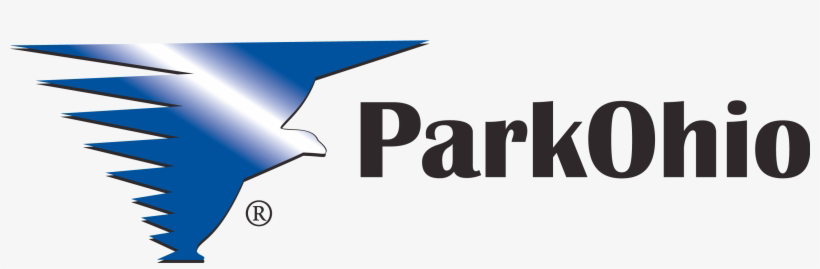
パーク・オハイオ社は、サプライチェーン管理のアウトソーシングサービス、生産ラインで使用される資本設備、製品の組み立てに使用される製造部品を世界クラスのお客様に提供する多角的な国際企業です。
- 時代遅れの旧式ERPシステム
- 正確な情報の欠如
- 手作業によるバッチプロセス
- 新たに買収した工場を迅速に統合する必要
- リアルタイム情報へのアクセス
- 自動化されたプロセス
- 品質管理の向上
- 不必要なコストの削減
- 収益性の向上
- リモート・データ・アクセス
マイク・ガーバー氏はパーク・オハイオ社の組立部品グループ(ACG)のITディレクターです。パーク・オハイオ社はサプライチェーン管理アウトソーシングサービス、生産設備、製造部品の多角的グローバルプロバイダです。
ACG部門は、自動車、農業機械、商用トラック、フォークリフト、エンジン、産業機器に使用される高度に設計された部品の大手メーカです。同事業部門は、米国、メキシコ、中国に19カ所の製造、組立、倉庫施設を有し、Plex ERP、Plex MES、およびMESオートメーション&オーケストレーション(A&O)を使用しています。Plexは2009年に最初に導入されました。
課題
時代遅れのERPシステムと情報の欠如
2008年の金融危機後、パーク・オハイオ社は困難な状況に陥りました。彼らは4つの工場を立ち上げる必要があり、ERPプロバイダとの契約は終了していました。
ガーバー氏は次のように述べています。「新しいERPシステムの導入は、切羽詰まった状況でした。私たちが直面した最大の課題の1つは、バッチ環境からよりリアルタイムな環境への移行でした。以前は、情報はバッチで収集され、コストを真に理解するのに十分な精度ではありませんでした。部品表はシステムで更新されていませんでした。しかし、情報が正確でなければ生産現場が停止してしまうようなリアルタイム環境で仕事をするようになると、適切なビジネス上の意思決定を行なうためには、より正確な情報が必要になります。」
パーク・オハイオ社は、世界中にある異なる4カ所の拠点に展開できる新しいシステムと、リアルタイムのオペレーションに必要な詳細レベルまで情報を追跡できるシステムを必要としていました。
ソリューション
ミスの多い手作業による工程を自動化
ACGはPlexを導入することで、面倒な紙ベースのミスが発生しやすいプロセスを自動化することができました。同部門がPlexを選択した理由は、短期間で工場をオンライン化できるクラウドベースのソリューションだったからです。
ガーバー氏は次のように説明します。「最初の4工場は6カ月で立ち上げに成功しました。Plexはクラウドベースの環境であるため、インフラに必要となる間接費がなく、非常に迅速に進めることができました。」
新規買収をシームレスに統合
Plexは、同部門のデジタルトランスフォーメーションとスマートマニュファクチャリング戦略の基盤となっています。また、ACGの急速な買収の成長を支える鍵にもなっています。
ガーバー氏は次のように述べています。「新しい工場を買収する際の私たちの目標は6カ月以内にPlexを導入することです。Plexは共通の情報プラットフォームを提供してくれます。既存の経営陣は、Plexとの付き合い方を熟知しており、新規買収の際も、買収先企業に情報を求め続ける必要はありません。また、一貫性のある情報を得ることで、より迅速な意思決定が可能になります。」
チェンジマネジメントの優先
ACGは、各施設のPlex導入におけるチェンジマネジメント(変更管理)を優先しています。彼らは、その工場の各機能を代表するメンバーでコアチームを結成します。
ガーバー氏は次のように説明します。「私たちの目標は、できるだけ多くの人を参加させることです。私たちは彼らを訓練し、システムのパイロットを何度も経験させます。彼らの古い習慣を断ち切り、これがリアルタイムであることを教え込むのです。彼らは生産に携わっています。問題を解決するために明日まで待つことはできません。」
結果
不必要なコストの削減
コスト把握の向上は、ACGにとってビジネス上の必須事項であり、Plexを使用した最も重要な成果の1つです。
ガーバー氏は次のように述べています。「最近、最後の3つのPlex導入が完了しました。今、これらの工場はコストを真に理解しており、材料、価格、労働効率の向上など、改善すべき点を理解することで、収益性の高いリターンを得ています。
製品品質の向上
品質の向上もACGにとってPlexのメリットの1つです。機械データをPlexに統合できるようになったことで、同部門はゴムホースの加硫工程でデータ主導のポカヨケを実現しました。加硫は、高品質で安全かつ耐久性のあるゴムホースを製造するために不可欠です。ポカヨケは、エラーを防止するための継続的な改善プロセスです。このアプリケーションでは、ACGがAllen‑Bradley®のPLCを使用してポカヨケを設計し、加硫不足のゴムが出荷されないようにしました。
ガーバー氏は次のように説明します。「通常、ポカヨケは1回の操作で終わります。ウィジェットを入れて、行くか行かないかです。しかし、統合することで、工場の端から端まで部品を追跡することができるようになり、工程に不具合があれば、次の工程を停止させることができます。」
加硫工程のエラーは、品質アラートのテキストメッセージで即座に通知され、ホースはシステムによって隔離されます。その後の作業でホースの使用は阻止され、出荷も阻止されます。
プロセスメトリクスのモニタ機能
同部門はまた、成分に細心の注意を払う必要があるゴム混合作業におけるリアルタイムのプロセスデータと使用量データにアクセスするためにPlexを使用しています。
ガーバー氏は次のように述べています。「オイルタンクのレベルをモニタすることは重要なので、バイヤーがリモートでレベルをモニタし、レベルが重要な再注文ポイントに達したときに警告メッセージを送信できるシステムを作りました。油切れを防ぐために工場に出向いて手作業で検針し、工場を停止させる必要はなくなり、デスクに座ってタンクレベルをチェックするだけでよくなりました。」
これらは、パーク・オハイオ社のACGがPlexを使用する革新的な方法のほんの一部であり、Plexの2023年のIndustry Leader Impact Awardに選ばれた理由です
公開 2024/10/28
お客様へのご提案