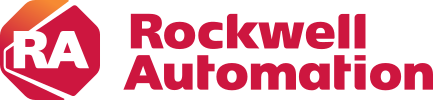
このストーリーは私たちについてです! ロックウェル・オートメーションは、産業オートメーションとデジタルトランスフォーメーションのグローバルリーダーです。ロックウェル・オートメーションは、人々の想像力とテクノロジの可能性を結びつけ、人間の可能性を広げます。
- 生産に支障をきたす前に、摩耗した工作機械による工程性能の低下を特定する。
- 消耗品の発見が最大30~60日早まる。
- 故障率が最大22%改善
- 人件費削減で4万5000ドルの節約
- 900万ドルの収益が早期に実現
タイヤがパンクすると何が起こるでしょうか? 通常、問題はすぐに警告されます。ダッシュボードに警告灯が表示されたり、運転中に違いを感じたりします。タイヤにパッチを当てるか交換すれば、問題なく運転を続けることができます。この問題はタイヤだけにとどまります。
しかし、多くの製造工程ではそうではありません。多くの場合、工具の一部が摩耗し始めると、工程に大きな中断が生じるまで、オペレータは介入が必要であることに気づきません。これは、ラインの追加部分が中断の対象となることを意味する可能性があります。ラインの製品が損傷したり、生産が停止することもあります。
オペレータがもっと早く個々の問題を特定できていれば、対策を講じることができたはずです。そのかわりに、製造業者はダウンタイム、材料の浪費、生産の損失を被ることになります。
ロックウェル・オートメーション、特にソフトウェアアーキテクトのカイ・リン、PBCAプロセスエンジニアのミキ・チヴィエティノヴィッチとグレゴリー・ヴァンスは、これがお客様にとっての問題であることを知り、何か対策を講じることを決意しました。彼らはオハイオ州ツインズバーグにあるロックウェル・オートメーションの製造工場でソリューションを試験的に導入しました。
課題
ロックウェル・オートメーションの各事業所におけるエレクトロニクス組立業務のスナップショットをご覧ください。
- 年間4000のユニークな回路基板設計を生産
- 1日当たり900万個の部品を配置
- 1日当たり2,300万個のはんだ接合を形成
- 1日当たり14000台のパネル生産
当社のツインズバーグの拠点には8つの製造ラインがあります。ツインズバーグは大規模な生産施設で、他の施設と同様、生産に影響を与える可能性のある多くの工程があります。試験的に、私たちは孔版印刷工程に焦点を当てることにしました。
プロセスを理解する
ステンシル箔にはレーザーでエッチングされた開口部があり、その下に回路基板が嵌合されます。その後、スクイージブレードではんだペーストをステンシルの前面から背面に押し出し、回路基板に付着するはんだペーストで開口部を埋めます。ストロークが終わると、回路基板が搬送され、検査されます。次の回路基板は、別のスクイージブレードで逆方向に印刷される。このプロセスの各部分で、性能データが生成されます。
見た目以上に複雑
一見単純に見える製造工程にも、隠れた複雑さがあります。第一に、ステンシル印刷工程は多くの独立した変数を持つ複雑なものです。そのため、サポートスタッフがステンシルやスクイージの磨耗や性能低下を検知するのは難しく、特に肉眼でその磨耗を確認するのが困難な場合はなおさらです。さらに、プロセスの開始時やプロセス中の長い休止時間は、ペースト転写の効果を変化させるため、ツールの長期的な摩耗を分析することを難しくしています。
さらに、より薄いステンシルや特殊なコーティングを施したステンシルは、寿命が異なるため、摩耗や破損の発生がさらに予測不可能になります。また、プロセスの各段階でパフォーマンスデータが生成されますが、サポートスタッフはこの膨大なデータ(IT、OT、およびエンジニアリング)をリアルタイムで収集・分析することができません。
サポートスタッフは、機器に関するリアルタイムのパフォーマンスデータを収集・分析し、機器の異常や破損を即座に警告するための優れた方法を必要としていました。これは、印刷検査から数秒後にFactoryTalk® DataMosaix™で計算され表示される、当社の異常検出アルゴリズムに最適な使用例でした。
ソリューション
当社のプロジェクトエンジニアとソフトウェアチームは、この課題に対してアルゴリズム的なアプローチをとりました。ロックウェル・オートメーションが所有する特許取得済みの異常検知アルゴリズムを作成し、孔版印刷工程における工具変更を監視して、サポートスタッフにパフォーマンスデータを送信しました。そして、そのアルゴリズムに通知を実装し、工場の担当者が面倒な事後分析を行なうことなく、異常に関するアラートを即座に受取ることができるようにしました。
タグとセンサの必要性
まずエンジニアリングチームは、各ステンシルとスクイージブレードにRFIDタグを追加し、ガントリーの移動方向を検知するセンサを取付けました。チームはそのデータを収集し、既存のプログラマブル・ロジック・コントローラー(PLC)が捕捉した機械に入るプリント基板のシリアル番号と結びつけた。また、データを対応するステンシルとスクイージに結びつけ、異常、欠陥、はんだ付け検査に関する性能データを取得しました。
エレガントなデータ収集とコンテキスト化
次に、FactoryTalk DataMosaixに目を向けました。 FactoryTalk DataMosaixは、さまざまなソースから大量の生データを取り込み、それを1つのプラットフォームにコンテキスト化して、運用管理チームが使用するアプリケーションに役立つように設計されたSaaSアプリケーションです。
FactoryTalk DataMosaixがこのプロジェクトに選択された理由は何でしょうか。一般的なBIツールは、このコンテキスト化をリアルタイムで実行する機能とともに、十分なデータ関係モデリングを提供していませんでした。例えばPower BIでは、誰かが手作業で分析を実行する必要がありました。
ツインズバーグの工場では、この分析は毎月行なわれていました。FactoryTalk DataMosaixを使用することで、この分析をリアルタイムで行なうことができます。
さらに、FactoryTalk DataMosaixは、スクイージブレードとステンシルが工場フロアを移動するときのライフサイクル全体を追跡します。通常、ステンシルが1つのラインで使用されると、そのデー タが追跡されます。 その後、ステンシルが別のラインに戻され、使用されるとき、ステンシルの過去のランタイムとパフォーマンスを示すデータは考慮されないため、担当者が潜在的なパフォーマンスの問題を見逃す可能性が高くなります。
FactoryTalk DataMosaixを使用して、機器故障のリスクを特定するチャートにデータをプロットしました。ロックウェル・オートメーションのソフトウェアアーキテクトであるカイ・リンは次のように述べています。「この分析方法は、「ラインのパフォーマンスを見る実にエレガントな方法」です。ラインが良くなっているのか、悪くなっているのかがよくわかります」。
Teams上でのリアルタイムアラート
最後に、チームはMicrosoft Teams上にチャンネルを構築し、工場内の誰もがそのチャンネルに登録することで、設備の異常や不具合に関する通知をリアルタイムで受取ることができるようにしました。アラートはさまざまな方法で生成することができました。私たちのチームがMicrosoft Teamsを使うことにしたのは、チームがすでに使っていた業務システムだったからです。
以前はこのプロセスがどのように機能していたかを説明します。はんだ付け検査機が回路基板の問題を検出した場合、オペレータは手作業でチェックやクリーニングを行なわなければならず、遅延や潜在的な判断ミスにつながっていました。現在では、スクイージやステンシルといったツール装置の性能を監視することで、アルゴリズムが基板の異常な高故障率に対するアラートを発し、オペレータに一時停止と迅速な問題調査を促しています。
以前は生産環境の性質上、問題の根源を特定することが難しかったが、導入されたソリューションのおかげで、オペレータは障害の原因となっている機器をすぐに特定できるようになりました。
そのときこそが、ソリューションが機能するかどうかを確認する時でした。工場は、2023年後半に、アルゴリズム、FactoryTalk DataMosaix、およびMicrosoft Teamsプロジェクトを稼動させ、約70日間データを収集しました。
課題
検査不良の減少
エンジニアリングチームと工場の担当者が、ステンシルの異常や欠陥に関する通知を受取り、それに応じて対応できた事例がいくつかありました。故障を待つかわりに(またはカレンダーの日付に基づいて無駄にステンシルを交換するかわりに)、アルゴリズムはオペレータにステンシル故障の30~60日前の警告を与えました。そして、それぞれの事例で破損したステンシルを交換または修理した後、故障率は22%改善しました。
オペレータの生産性向上
さらに、機械オペレータの生産性も向上しました。他の生産ラインに影響を及ぼす前に、サポート担当者にステンシルの問題が通知され、有意義なデータが得られるようになり、有意義なデータを扱うことができると、オペレータは注意散漫になることが少なくなり、より効率的に仕事ができるようになりました。
ツインズバーグとその先のROI
ツインズバーグの施設で4カ月間評価した結果、年間労働力の節約はコストを劇的に上回り、ROIは約200%でした。さらなる使用例が計画されているため、FactoryTalk DataMosaixのROIはさらに増加し、この年間費用を正当化できると確信しています。
新たな収益
最後に、故障率の改善と生産性の最大化は、収益の向上につながりました。具体的には、中断が少なくなったことで、工場は900万ドル相当の収益を早期に実現できるようになりました。
未来は明るい...そして生産的
アルゴリズムとFactoryTalk DataMosaixの統合の将来はどうなるのでしょうか? エンジニアリングチームとソフトウェアチームは、ツインズバーグ、メコン、モントルー、シンガポールの工場で、このソリューションを大規模に展開するために取り組んでいます。また、このソリューションの他のアプリケーションも探しています。
ロックウェル・オートメーションはこのアルゴリズムを所有しているため、お客様にとっての使用ケースはまさに無限です。カイ・リンが言うように、「アルゴリズムが何を提供するのか...そして、それをプロセスにおける工具変更の性能モニタに本当に関連付けることを考えると、ディスクリート製造において非常に広い適用可能性が見えてきます。」
オペレータの生産性向上
さらに、機械オペレータの生産性も向上しました。他の生産ラインに影響を及ぼす前に、サポート担当者にステンシルの問題が通知され、有意義なデータが得られるようになり、有意義なデータを扱うことができると、オペレータは注意散漫になることが少なくなり、より効率的に仕事ができるようになりました。
ツインズバーグとその先のROI
ツインズバーグの施設で4カ月間評価した結果、年間労働力の節約はコストを劇的に上回り、ROIは約200%でした。さらなる使用例が計画されているため、FactoryTalk DataMosaixのROIはさらに増加し、この年間費用を正当化できると確信しています。
新たな収益源
最後に、故障率の改善と生産性の最大化は、収益の向上につながりました。具体的には、中断が少なくなったことで、工場は900万ドル相当の収益を早期に実現できるようになりました。
未来は明るい...そして生産的
アルゴリズムとFactoryTalk DataMosaixの統合の将来はどうなるのでしょうか? エンジニアリングチームとソフトウェアチームは、ツインズバーグ、メコン、モントルー、シンガポールの工場で、このソリューションを大規模に展開するために取り組んでいます。また、このソリューションの他のアプリケーションも探しています。
ロックウェル・オートメーションはこのアルゴリズムを所有しているため、お客様にとっての使用ケースはまさに無限です。カイ・リンが言うように、「アルゴリズムが何を提供するのか...そして、それをプロセスにおける工具変更の性能モニタに本当に関連付けることを考えると、ディスクリート製造において非常に広い適用可能性が見えてきます。」
公開 2024/06/26