「古いマシンを複製する一方で、信じられないほど短い時間枠で現在の制御および安全基準に合わせて最新化する必要もあります。スケジュールが非常にタイトであるため、通常6か月かかることを実行するのに8週間しかありません」と、Foodmach社のCEOであるアール・ロバーツ氏は説明します。
パンデミックの最中、世界保健機関(WHO)は、需要の高まり、パニック買い、買い占め、誤用などにより、個人防護具(PPE)の世界的な供給に深刻な混乱が生じており、人命が危険にさらされていると警告しました。
この問題に対処するため、WHOは産業界と政府に対し、この世界的な需要の高まりに対応するため、製造量を40%増加させるよう呼びかけました。
この目標を達成するために、世界中の製造メーカや機械装置メーカ(OEM)が立ち上がりました。オーストラリアでは、連邦政府が当時唯一の地元マスクメーカであったMed-Con社に、この需要に応えるための増産を要請しました。しかし、40年前に作られた3台の機械のうち2台しか稼働しておらず、これを実現するためにはマスク製造機の増設が急務であると考えました。
地球の反対側のニュージャージー州モントヴィルにあるキャットブリッジ・マシナリー社は、COVID-19に対して、材料不足という緊急のニーズに応えるターンキーソリューションを提供しました。現在、同社は北米に拠点を置くターンキーのメルトブローン生産ラインの唯一のサプライヤです。
マスクの素材づくり
メルトブローン不織布は、N95マスクやろ過材に欠かせない素材です。ポリプロピレンを原料とするこの高機能素材は、厳しいろ過仕様を満たすように設計されています。
キャットブリッジ・マシナリー社の社長であるマイケル・パパス氏は次のように述べています。「当社の専門分野の1つはメルトブローン生産ラインを含む不織布加工です。当社は、材料不足に対応できるソリューションをパッケージ化する作業にすぐに取り掛かりました。」
一般的な濾過材の規格を満たすために、同社は織物の幅1.6メートル(5.2フィート)のソリューションをパッケージ化しました。ターンキー生産ラインは、メザニンレベルとプラントレベルの両方の機器を備えており、押出成形、メルトブローン成形システム、織物処理装置、すべての機械的接続、制御パッケージ、電気パネルが含まれています。
メルトブローン生産ラインは、Allen‑BradleyのGuardLogixセーフティコントローラおよびAllen‑Bradley Kinetixサーボドライブとモータを搭載したロックウェル・オートメーションの制御プラットフォームで稼働しています。システムはEtherNet/IP™ネットワークで統合されます。
パパス氏は次のように述べています。「通常、当社では機械のHMIにグラフィックターミナルを使用します。しかし今回は、Allen‑BradleyのVersaView産業用PCおよびモニタを選択しました。」
堅牢なVersaView製品は、アプリケーションのソースでより多くのコンピューティングパワーを提供し、画面から何にアクセスして管理できるかという柔軟性を提供します。このケースでは、システムにFactoryTalk View Site Edition (SE) HMIソフトウェアが搭載されており、複数の関係者の要求を満たすことができます。
オペレータは、表示画面、アラーム、システム全体の診断に簡単にアクセスできます。また、メンテナンスやエンジニアリングについては、アプリケーションを迅速に開発し、システムのメンテナンスを容易に行なうことができます。
パパス氏は次のように述べています。「COVID-19のパンデミックは、多くの人にとってジェットコースターのようなものでした。N95マスクはいまだに不足していますが、これから何が主流になるのでしょうか? 私たちには分かりません。このような不確実な時代には、機械の柔軟性は性能と同じくらい重要です。」
救命用マスク製造機の製作
オーストラリア政府の支援を受け、オーストラリアのビクトリア州に拠点を置く高度な受注生産企業であるFoodmach社が選ばれました。オーストラリア政府の支援を受けて、Foodmach社は、2020年11月までに6000万枚のフェイスマスクを生産し、年間1億6000万枚のマスクを生産することを目標に、緊急の供給需要を満たすために7台の救命機械の最初の設計と製造に60日の期限を与えられました。
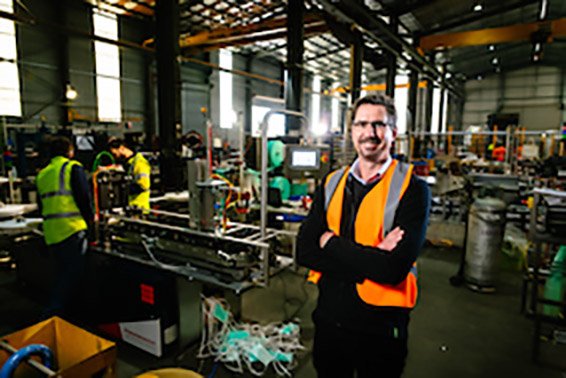
Foodmach社のCEOのアール・ロバーツ氏、工場の現場で
Foodmach社は元の機械機構を採用し、ロックウェル・オートメーションの最新の制御および自動化技術を搭載するようにそれらを最新化することができました。Allen‑BradleyのCompact GuardLogixコントローラはマシンの中心であり、マスクの製造プロセスを制御します。
Kinetix 5500サーボドライブはLogixプラットフォームにシームレスに統合され、簡単な構成、システム統合、および安全を実現します。PLCとサーボドライブはともに、機械内の動きを制御し、機械の始動と停止機能の精度を維持するための鍵となります。
これらのマシンは、優れた保護のために4つの層が一緒にラミネートされた最高品質のサージカルマスクを構築するように設計されています。Allen‑Bradleyの安全トルクオフを備えたPowerFlex 525ドライブは、ラミネーション(積層加工)プロセスを制御している間、オペレータはマシンのPanelView™グラフィックターミナルを使用して生産をモニタできます。
アール・ロバーツ氏は次のように述べています。「最初のマシンを8週間で製造することを目指していましたが、7週間で予定より早く納品することができました。その重要な部分は、オーストラリアで利用可能な部品の在庫を保持し、必要に応じて海外からのコンポーネントの取り込みを促進できるロックウェル・オートメーションなどのサプライヤを持つことでした。」
オーストラリアのマスク製造能力は、エンジニア、設計者、技術者の卓越したチームの革新的な仕事のおかげで確保されています。これらのスマートマシンは、マスクの生産を大幅に増やす能力を提供し、COVID-19の撲滅に向けて最前線で働く医療従事者や作業者とその患者を守ることができます。
デジタル化による視認性の向上
機械や材料の不足によるサプライチェーンの問題に対処することに加え、産業界にとってもう1つの重要な焦点はオペレーションの効率化です。デジタルトランスフォーメーションは接続性と可視性を向上させ、最終的にパフォーマンスと効率を改善します。
エコラボ社は、水、衛生、感染予防のためのソリューションとサービスを提供するグローバルリーダです。世界各地に130の工場を持つエコラボ社は、世界中の約300万のお客様の施設で、食品衛生の向上、清潔で安全な環境の維持、水とエネルギーの使用量の最適化を支援しています。しかし最近まで、これらの工場は互いに連携が取れておらず、一貫性に欠けていました。その結果、各工場は基本的に独立した存在として機能していました。
現在、エコラボ社のグローバルな工場ネットワークは、より優れたパフォーマンスと安定性を実現し、最終的に顧客により良いサービスを提供できるよう、5年間のロードマップに沿ってより優れた接続性を実現しています。
エコラボ社の制御および自動化プログラムのリーダであるマット・ブジューク氏は同社のデジタルトランスフォーメーションを主導するために採用されました。
ブジューク氏は次のように述べています。「私の仕事は、制御スキームを改善するだけでなく、知識の導管となり、プラント間で知識を共有することです。私たちの会社は良い規模の会社で、お互いに話し合っていなければ利用できてはいないでしょう。」
チームはエコラボ社の工場をデジタル化するための4つのステップの戦略を策定しました。まず、最初はデータ収集のステップです。これには、適切な機器を設置し、適切なデータを収集することが含まれます。この段階では、後の段階でデータを特定して分析できるようにするために、文書化が重要です。
次のステップは可視性で、プラントでオペレーションのモニタを開始し、ダッシュボードにより、オペレータがラインのパフォーマンスをリアルタイムで把握できるようになります。3番目のステップはビジネスの最適化です。これには、プラントフロアを企業の基幹システムと統合して、プラントとサプライチェーン全体の可視性とコミュニケーションを提供することが含まれます。
4つ目と最後のステップは、分析、デジタルツイン、人工知能などを活用したデジタルトランスフォーメーションです。これにより、ある工場のパフォーマンスが他の工場よりも優れている理由など、重要な疑問に答えることができるようになります。
すでに今日、いくつかのプラントは最適化段階にあります。また、標準化の取り組みとグローバルな可視性の向上により、同社はプロセス設計を25~30%節約できました。在庫と手持ちの日数をより適切に処理することも、改善の大きな機会です。
エコラボ社はベンダーと協力して、一部の工場ではオンサイトのトレーニングラボを含むトレーニングプログラムを確立し、従業員が新しいテクノロジに触れて学べるようにしました。
ブジューク氏は次のように述べています。「結局、コミュニケーションと全員の賛同が重要なのです。みんなが参加して、自分にも発言権があると思えば、プロジェクトにも積極的に参加し、一緒になって取り組むことができます。なぜなら、それによって自分の生活が楽になることを知っているからです。」