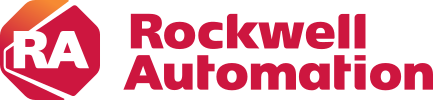
이 글은 로크웰 오토메이션에 대한 글입니다!
로크웰 오토메이션은 산업 자동화 및 디지털 트랜스포메이션 분야의 글로벌 리더입니다. 우리는 사람들의 상상력과 기술의 잠재력을 연결하여 인간의 가능성을 확장합니다.
- 마모된 툴링 장비로 인한 공정 성능 저하가 생산 중단으로 이어지기 전에 파악
- 마모된 품목 최대 30~60일 조기 감지
- 불량률 최대 22% 개선
- 인건비 절감으로 $45,000 절감
- 9백만 달러의 수익 조기 실현
타이어 펑크의 비교적 긍정적인 면은 무엇일까요? 보통 문제를 즉시 알 수 있다는 점입니다. 대시보드에 경고등이 표시되거나 운전할 때 타이어에 이상이 느껴집니다. 타이어를 패치하거나 교체하고 문제 없이 운전을 계속합니다. 문제는 타이어에만 국한된 상태로 유지됩니다.
많은 제조 공정에서의 경우 그렇지 않습니다. 툴링 부품이 마모되기 시작하면 작업자는 공정에 더 큰 중단이 발생할 때까지 개입이 필요하다는 사실을 인지하지 못하는 경우가 많습니다. 이는 라인의 다른 부분도 중단될 수 있음을 의미할 수 있습니다. 라인의 제품이 손상될 수 있고, 생산이 중단될 수도 있습니다.
운영자가 개별 문제를 더 일찍 파악할 수 있었다면 조치를 취할 수 있었을 것입니다. 대신 제조업체는 가동 중단 시간, 자재 낭비, 생산 손실을 입게 됩니다.
로크웰 오토메이션, 특히 소프트웨어 설계자인 카이 린(Kai Lin)과 PBCA 프로세스 엔지니어인 미치 치제티노비치(Miki Cvijetinovic)와 그레고리 밴스(Gregory Vance)는 이 문제가 고객의 문제라는 것을 알고 이를 해결하기 위해 무언가를 하기로 결정했습니다. 이들은 오하이오주 트윈스버그에 있는 로크웰 오토메이션 제조 공장에서 솔루션을 시범 운영했습니다.
Challenge
다음은 로크웰 오토메이션 시설 전반의 전자 조립 작업에 대한 스냅샷 입니다:
- 연간 4K 개의 고유 회로 기판 설계 생산
- 하루 9백만 개의 부품 배치
- 하루 2300만 개의 납땜 작업
- 하루 14,000 개의 패널 생산
트윈스버그 지사에는 8개의 제조 라인이 있습니다. 트윈스버그는 대규모 생산 시설로, 모든 시설과 마찬가지로 생산에 영향을 미칠 수 있는 많은 공정이 있습니다. 이번 파일럿에서는 스텐실 인쇄 공정에 초점을 맞추기로 했습니다.
프로세스 이해
스텐실 포일에는 레이저로 에칭된 구멍이 있으며, 그 아래에 회로 기판이 결합된니다. 그런 다음 스퀴지 블레이드가 스텐실의 앞쪽에서 뒤쪽으로 땜납 페이스트를 밀어내여 구멍에 땜납 페이스트를 채워 회로 기판에 침전되어 달라붙게 합니다. 스트로크가 끝나면 회로 기판을 옮긴 다음 검사 합니다. 다음 회로 기판은 다른 스퀴지 블레이드를 사용하여 반대 방향으로 인쇄됩니다. 이 과정의 각 부분에서 성능 데이터가 생성됩니다.
눈에 보이는 것보다 더 복잡한 과정
단순해 보이는 제조 공정과 마찬가지로 숨겨진 복잡성이 있습니다. 첫째, 스텐실 인쇄 공정은 독립적인 변수가 많아 복잡합니다. 이로 인해 지원 담당자가 스텐실과 스퀴지의 마모나 성능 저하를 감지하기 어렵고, 특히 육안으로 확인하기 어려운 마모를 감지하기 어렵습니다. 또한 공정 시작과 공정 중 긴 일시 정지는 페이스트 이송의 효율성을 변화시켜 툴링의 장기 마모를 분석하기 어렵게 만듭니다.
또한 더 얇거나 특수 코팅이 된 스텐실은 수명이 다르기 때문에 마모를 더욱 예측할 수 없습니다. 또한 공정의 각 단계에서 성능 데이터가 생성되지만 지원 담당자는 IT, OT, 엔지니어링 등 방대한 양의 데이터를 실시간으로 수집하고 분석할 수 없습니다.
지원 담당자는 장비의 실시간 성능 데이터를 수집 및 분석하고 장비 이상이나 손상에 대해 즉시 알림을 받을 수 있는 더 나은 방법이 필요했습니다. 이는 이상 감지 알고리즘의 완벽한 사용 사례였으며, 인쇄 검사 후 몇 초 만에 FactoryTalk® DataMosaix™를 통해 계산 및 표시할 수 있었습니다.
Solution
프로젝트 엔지니어와 소프트웨어 팀은 이 문제를 알고리즘으로 접근했습니다. 이들은 스텐실 인쇄 공정에서 툴링을 모니터링하고 지원 직원에게 성능 데이터를 전송하는 로크웰 오토메이션의 특허받은 이상 감지 알고리즘을 개발했습니다. 그런 다음 이 알고리즘에 알림 기능을 구현하여 공장 직원이 지루한 사후 분석을 수행할 필요 없이 이상 징후에 대한 즉각적인 알림을 받을 수 있도록 했습니다.
필요한 태그 및 센서
먼저 엔지니어링 팀은 갠트리가 움직이는 방향을 감지하는 센서와 함께 각 스텐실과 스퀴지 블레이드에 RFID 태그를 추가했습니다. 이 팀은 데이터를 수집하여 기존 PLC(프로그래머블 로직 컨트롤러)로 캡처한 기계에 들어가는 인쇄 회로 기판의 일련 번호와 비교했습니다. 또한 데이터를 해당 스텐실과 스퀴지에 연결하여 이상, 결함 및 땜납 페이스트 검사에 대한 성능 데이터를 얻었습니다.
탁월한 데이터 수집 및 컨텍스트화
다음으로 FactoryTalk DataMosaix를 사용했습니다. FactoryTalk DataMosaix는 다양한 소스에서 대량의 원시 데이터를 가져와 하나의 플랫폼으로 컨텍스트화하여 운영 관리 팀에서 사용하는 애플리케이션에 유용하게 사용할 수 있도록 설계된 SaaS 애플리케이션입니다.
이 프로젝트에 FactoryTalk DataMosaix를 선택한 이유는 무엇인가요? 일반적인 비즈니스 인텔리전스(BI) 도구는 이러한 컨텍스트화를 실시간으로 수행하는 기능과 함께 충분한 데이터 관계 모델링을 제공하지 못했습니다. 예를 들어, Power BI는 누군가가 수동으로 분석을 수행해야 했습니다.
트윈스버그(Twinsburg) 공장의 경우, 이 분석은 매월 수행되었습니다. FactoryTalk DataMosaix를 사용하면 실시간으로 분석을 수행할 수 있어 공장 직원에게 성능 이상 징후를 즉각적으로 알릴 수 있습니다.
또한 FactoryTalk DataMosaix는 스퀴지 블레이드와 스텐실이 공장 바닥에서 이동할 때 전체 수명 주기를 추적합니다. 일반적으로 스텐실이 한 라인에서 사용되면 해당 데이터가 추적됩니다. 나중에 스텐실을 다시 가져와 다른 라인에 배치할 때는 스텐실의 과거 런타임과 성능을 알려주는 데이터가 고려되지 않으므로 직원이 잠재적인 성능 문제를 놓칠 가능성이 높아집니다.
FactoryTalk DataMosaix를 사용하여 장비 고장 위험을 식별하는 차트에 데이터를 플로팅했습니다. 로크웰 오토메이션의 소프트웨어 아키텍트인 카이 린(Kai Lin)은 이 분석 방법이 "라인의 성능을 살펴볼 수 있는 정말 우아한 방법"이라고 말합니다. "라인이 개선되고 있는지 또는 악화되고 있는지를 알려줍니다."라고 말합니다.
Teams의 실시간 알림
마지막으로 이 팀은 공장의 모든 사람이 구독하여 장비 이상이나 결함에 대한 실시간 알림을 받을 수 있는 채널을 Microsoft Teams에 구축했습니다. 알림은 다양한 방법으로 생성할 수 있었습니다. 우리 팀은 팀에서 이미 사용하고 있던 비즈니스 시스템이기 때문에 Microsoft Teams를 사용하기로 결정했습니다.
프로세스는 다음과 같이 진행되었습니다. 땜납 페이스트 검사 기계가 회로 기판의 문제를 감지하면 작업자가 수동으로 확인하거나 청소해야 했기 때문에 작업이 지연되거나 판단 오류가 발생할 가능성이 있었습니다. 오늘날에는 스퀴지 및 스텐실과 같은 툴링 장비의 성능을 모니터링하여 기판의 비정상적으로 높은 고장률에 대해 알고리즘이 경보를 발동하여 작업자가 작업을 일시 중지하고 문제를 즉시 조사하도록 유도합니다.
이전에는 생산 환경의 특성상 문제의 원인을 파악하기 어려웠지만, 솔루션을 도입한 덕분에 운영자는 장애를 일으키는 장비를 빠르게 식별할 수 있게 되었습니다.
이제 솔루션이 제대로 작동하는지 확인할 차례였습니다. 이 공장은 2023년 말에 알고리즘, FactoryTalk DataMosaix 및 Microsoft Teams 프로젝트를 가동하고 약 70일 동안 데이터를 수집했습니다.
Result
Reduction in Failed Inspections 검사 실패율 감소
엔지니어링 팀과 공장 직원이 스텐실 이상 또는 결함에 대한 알림을 받고 적절히 대응할 수 있었던 사례가 여러 차례 있었습니다. 이 알고리즘은 고장을 기다리거나 달력 날짜에 따라 스텐실을 교체하는 낭비 대신 작업자에게 스텐실 고장에 대한 30~60일 전 사전 경고를 제공했습니다. 그리고 각 경우에 손상된 스텐실을 교체하거나 수리한 후 고장률이 22% 개선되었습니다.
Improved Operator Productivity 작업자 생산성 향상
또한 기계 운영자의 생산성도 향상되었습니다. 이제 지원 담당자는 스텐실 문제가 나머지 생산 라인에 영향을 미치기 전에 경고를 받고 의미 있는 데이터를 활용하여 작업할 수 있으며, 작업자는 방해 요소가 줄어들어 더욱 효율적으로 작업할 수 있습니다.
트윈스버그 및 그 밖의 지역의 ROI
트윈스버그 시설에서 4개월간 평가한 결과, 연간 인건비 절감액이 비용보다 훨씬 높았으며, 약 200%의 ROI를 달성한 것으로 계산되었습니다. 추가 사용 사례를 계획하고 있으므로 FactoryTalk DataMosaix의 ROI는 더욱 증가하여 연간 비용을 정당화할 수 있을 것으로 확신합니다.
수익 창출
마지막으로, 고장률 개선과 생산성 극대화는 매출 향상으로 이어집니다. 구체적으로 이 공장은 가동 중단이 줄어들어 900만 달러 상당의 수익을 더 빨리 실현할 수 있었습니다.
미래는 밝고... 또한 생산적입니다.
알고리즘과 FactoryTalk DataMosaix 통합의 미래는 어떻게 될까요? 엔지니어링 및 소프트웨어 팀은 트윈스버그뿐만 아니라 메콘, 몬테레이, 싱가포르 공장에 대규모로 배포하기 위해 노력하고 있습니다. 또한 자체 사업장 내에서 이 솔루션의 다른 적용 사례도 모색하고 있습니다.
로크웰 오토메이션이 알고리즘을 소유하고 있기 때문에 고객을 위한 사용 사례는 정말 무궁무진합니다. "알고리즘이 무엇을 제공하는지 생각해보고 이를 공정에서 툴링의 성능 모니터링과 연관시켜 보면 이산형 제조에 매우 폭넓게 적용될 수 있을 것입니다."라고 카이 린은 말합니다.
Published 2024년 6월 27일