お客様へのご提案
課題
- スウェーデンの真鍮部品メーカは、真鍮部品のスタンピングのためにコンパクトなホットスタンピングと切断システムを求めていました。
ソリューション
- Allen‑BradleyのControlLogix 1756プログラマブル・オートメーション・コントローラ(PAC)
- Allen‑BradleyのKinetix 5700サーボドライブ
- Allen‑BradleyのPowerFlex 525および755 ACドライブ
- Allen‑BradleyのPOINT I/O
- FactoryTalk View Studio SE 9.0
結果
- 必要に応じて電気軸と油圧軸の新しい動作をより迅速に実装
- お客様の施設での立上げのための機械セットアップ時間を短縮
- ガス炉使用時のエネルギー消費コストを50%削減
- ケーブル配線時間と機械チェックに関して人件費を20%削減
- 最終顧客での、製造された部品の生産と品質の向上
背景
ネオテックマンは、忍耐力、達成力、および不利な状況で戦ってきたという歴史を持っています。その起源は、家族経営の鍛造事業であるMetalúrgica Domingoに由来します。マネージャであるマネル・ドミンゴ氏は、生産を改善する油圧モデルを開発するようにそのパワープレスのサプライヤに訴えることにうんざりして、自社で使用するために7台の実用レベルの試作機を自分で設計して製造することに決めました。これらの試作機によって、同社は一月に最大350万ユニットの生産量を達成することができ、直近2年間は24時間ノンストップで稼働しています。
試作機の成功後、ドミンゴはネオテックマンを立ち上げ、この自動装置の開発、製造および販売に専念するために、2004年にファミリービジネスを離れて、産業機械メンテナンスのエキスパートであるカルレス・エステベ社と提携することを決定しました。
スペインのジローナにある同社は、それ以来、非鉄ホット・ブラス・スタンピング自動油圧システムの製造におけるパイオニアであり、世界的リーダとなっています。現在、タップ、継手、水とガス用のボール・チェック・バルブ、エルボー、ナットなどを目的とした要素を製造するための油圧スタンパを展開するさまざまな業界をカバーする多様な世界的な顧客ポートフォリオを持っています。
そのうちの一社は、真鍮部品の製造を専門とするスウェーデンの会社です。この会社は、製造された真鍮部品のコンパクトなホットスタンプおよび切断システムを提供しているので、ネオテックマンの機械の1つに投資することを決定しました。
課題
この場合の課題は、生産性、特に製造部品の品質を高めるために、お客様の生産ニーズに応じてネオテックマンのスタンパの油圧と電気サーボドライブの使用を設定することでした。
これらのスタンパは、バーの装填と加熱から始まる非鉄金属の自動および継続的な鍛造プロセスを実施します。鍛造温度に達したら、ブランク(金属片)をホットカットして金型に入れ、そこでパンチがブランクを希望する形状に成形します。最後に、金型を開いて最終鍛造品を取り出します。これは炉と切断システムを含むバリのない油圧システムによるコンパクトなプロセスです。これに加えて、振動が発生しないため、加工エリアの近くに配置することができます。
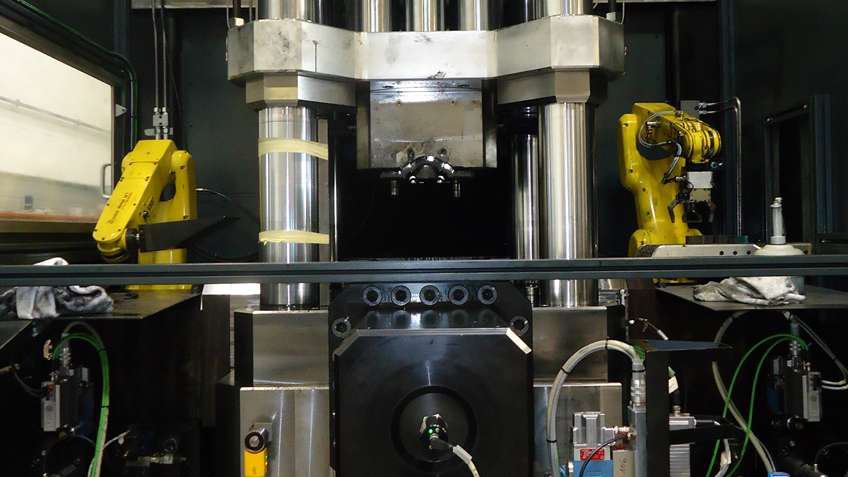
真鍮部品の油圧動作のすべてをシームレスに操作できるサーボドライブ、サーボバルブ、PLCなどの高品質なコンポーネントを利用できることは、スタンパー生産を最適化する上で非常に重要なことでした。
お客様の生産性を向上させるために、油圧部品はこれらの機械において重要です。ほとんどの油圧運動は、MOOGサーボバルブによって制御されます。
そのうちの1つはRAMを下げて、最大5つの内蔵パンチを動かして材料を形成する前に金型を閉じることができます。これらのパンチは最大毎分2,000リットルの流量を可能にするサーボバルブによって制御されます。0.01mmの精度で1,200mm/secのピーク速度まで移動することができます。ネオテックマンのテクニカルチームによると、「この速度は、最大300barのメインチャンバー内の油圧と共に運動エネルギーに変換され、材料を成形して目的の形状を実現するための大きな衝撃をもたらします。」
これらの機械のパンチの高速に加えて、これらはPLC内の電子カムによってリンクされているため、カム内の各ピストンはその速度と距離と共に移動すると予想されるタイミングでプログラムできます。
この意味で、PLCによる非常に高速なデータ収集が重要であり、設定する時間、速度、および圧力が単純化されるため、この製品の最終結果はお客様の要件を満たします。
このスウェーデンの製造メーカの設備でスタンパの生産を最適化するためには、サーボドライブ、サーボバルブ、PLCなど、真鍮部品のすべての油圧動作をシームレスに稼動できる高品質の部品を入手することが重要でした。
ソリューション
ネオテックマンは、ロックウェル・オートメーションの制御ソリューションから製品を導入することを決めました。テクニカルチームは次のように説明しています。「最初は、アメリカのお客様からの要求でしたが、アプリケーションの複雑な性質のため、その導入には多大な労力を必要としました。ただし、機械の応答時間の大幅な改善とプログラミングの合理化により、その利点はすぐに明らかになりました。その瞬間から、当社のすべてのモデルにロックウェル・オートメーションの技術を採用することを決めました。」
ロックウェル・オートメーションは、Allen‑BradleyのControlLogix 1756プログラマブル・オートメーション・コントローラ(PAC)、Allen‑Bradley®のKinetix® 5700サーボドライブ、Allen‑Bradley PowerFlex® 525および755 ACドライブ、および軸制御モジュール、サーボバルブの位置を非常に正確に制御できるようにする他のコンポーネントを提供しています。
また、機械の安全ソリューションは、Allen‑BradleyのPOINT I/O™を使用してプロセスPACに安全ロジックを導入することによっても簡素化されます。さらに、ネオテックマンのテクニカルチームは次のように述べています。「FactoryTalk® View Studio SE SCADAとSQLデータベースによって、イベント履歴、診断、およびエネルギー消費を監視できます。」
ロックウェル・オートメーションの製品は各ピストンの電子カムにも使用され、ピストンが動き始めるタイミングとその速度と距離を示します。
EtherNet/IP™を介してPLCに接続された2台の7kgロボットは、スウェーデンの会社の施設でスタンパの供給と形成部品を取り外すために使用されます。ネオテックマンのテクニカルチームは次のようにコメントしています。「ロックウェル・オートメーションのLogix環境にはロボットと通信するためのコードブロックが用意されているため、通信は非常に簡単です。これにより多くの時間を節約できました。それに加えて、SCADAを使用してロボットを直感的にプログラムするインターフェイスを開発しました。これにより、オペレータによるエラーの可能性がほぼなくなりました。」
結果
テクニカルチームは次のよう述べています。「ロックウェル・オートメーションのコンポーネントにより、ネオテックマンの機械の新しい電気軸と油圧軸を素早く実装することができました。油圧軸または電気軸の追加など、スタンパの変更をお客様から依頼された場合は、プログラミングと設置の両方でシステムへの実装が迅速になります。」
コンドム氏は次のように述べています。「このスウェーデンのお客様がそのニーズに従ってそれを設定するためにスタンパの修正を要求したときに、システムへの実装はプログラミングと設置時間の両方の点で非常に迅速でした。」
同様に、すべてのモータとロボットの位置決めが簡単かつ迅速に設定できるため、機械セットアップ時間も短縮されました。マネージャは次のように述べています。「この意味で、簡単な設計は、SCADAシステムと、ロックウェル・オートメーションのソリューションとロボットとの通信を簡単にしてくれました。これによって、すべての軸が自動的に位置決めされるため、機械内の部品のセットアップ時間を短縮できます。」
同様に、Rockwell Automation®のIntegrated Architecture® (統合アーキテクチャ)システムによってネオテックマンの機械部品の動作速度が向上したため、最終顧客は生産量を増やし、製造品の品質を向上することができました。これは、生産率の低さや製品の品質に関連した欠点など、産業組織における実際の問題を改善するのに、ロックウェル・オートメーションの統合アーキテクチャシステムが役立った方法です。
それだけではありません。プロセスおよび安全信号にPOINT I/Oを使用すると、コントローラをアクチュエータの近くに配置できるため、ネオテックマンはケーブル配線を減らすことができます。特に、「ケーブル配線時間と機械のチェックに関して、人件費が20%削減されました。より迅速でより効率的なプロセスになりました」と、マネージャは付け加えます。
ロックウェル・オートメーションのコンポーネントの制御システムの応答とネオテックマンが設計した油圧ディストリビュータにより、お客様の施設で機械の電力消費も削減されました。
「これは、それぞれ最大100mmの移動量を持つ、部品を形作る5つのパンチの圧力を制御することによって達成されました。高圧(300bar)はビレットを変形するためにのみ使用されるため、エネルギーの節約は非常に重要です。ストロークとビレットとの最初の接触を実行するには、中程度の圧力を使います。パンチがビレットとの接触を開始すると(シリンダの圧力が急激に増加するため)、高圧が発生します。このように、ストロークの終わりにしか高圧を使う必要がなくなりました。」
お客様には他にも利点があります。例えば、ネオテックマンのテクニカルチームは「ガス炉を使用すると、バーを加熱するためのコストは50%削減されます」と、語っています。これは、4mの真鍮バーをセットポイントから±5℃の温度に保つことで達成されます。パイロメータは温度を測定し、このデータをコントローラに送ります。コントローラはバーナーを自動的に調整して、バー全体を安定した温度に保ちます。さらに、機能的な設計とプロセスオートメーションによって、金型の切換え時間が大幅に短縮し、スタンピングプロセスのノイズレベルが大幅に低下します。これらの機械は人件費の節約にもなります。プロセス全体に必要なオペレータは1人だけで十分です。物流では、1つの資材の積み込みおよび積み降ろし用ベイが1つの作業領域で済みます。
最後に: 「キャビネットは機械に統合されているため、お客様の施設での立上げは非常に迅速にできます。スウェーデンのお客様は、電力供給、炉の燃料(天然ガスまたはプロパン)、および空気供給だけを必要としています。これらはネオテックマンの施設で以前に作成され確認されているため、追加の接続は必要ありません。」また、可能な限りお客様を支援するために、この機械にはiPadとSkypeのアカウントが含まれています。そのため、オペレータは必要に応じてネオテックマンのテクニカルサポートに連絡したり、発生状況に関する画像を表示できます。
Allen‑Bradley, ControlLogix, FactoryTalk View Studio, Integrated Architecture, Kinetix, LISTEN. THINK. SOLVE., POINT I/O, PowerFlex, PanelView Plus, Rockwell Automation, およびStudio 5000は、Rockwell Automation, Inc.の商標です。
EtherNet/IPは、ODVA Inc.の商標です。
Rockwell Automationに属していない商標は、それぞれの企業が所有してます。
公開 2017年8月29日